Marine fenders are available in a variety of styles - each one has its own purpose and they’re suitable for a wide array of boats and mooring conditions. When choosing the right fendering application, you must make the right decision. Otherwise, you’ll be exposing your boat to potential damage without an adequate level of protection.
It’s thought, the average boat is replaced between 10 and 20 years. However, with the right fendering type, you can maximise the longevity of your vessel and ensure that any damage is minimised. Not only is applying the correct marine fender type important but regularly maintaining and replacing them too.
So, what are the different types of marine fenders? And what are the key differences between each style? Don’t worry if you’re unsure - this post will explain everything you need to know. That way, when it comes to choosing the right fendering application for your needs and requirements, you can make a more informed decision.
We’ll cover:
RECAP: What is a Marine Fender?
Cell Marine Fenders
Cone Marine Fenders
Pneumatic Marine Fenders
Arch Marine Fenders
Pile Marine Fenders
RECAP: What is a Marine Fender?
Cell Marine Fenders
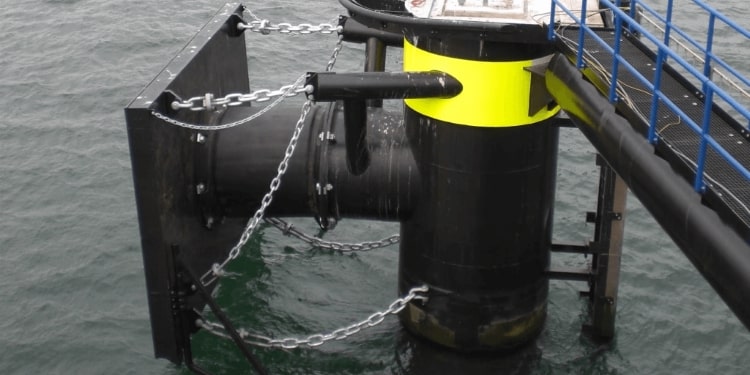
Key Fender Features:
Easy installation.
High-performance strength.
Low reaction force.
Innovative and excellent design for longevity.
Wear-resisting.
Can deflect up to 50 percent of the force in an axial direction.
Recommended Fender Applications:
Oil and LNG facilities.
Bulk terminals.
Offshore platforms.
Container berths.
RoRo and cruise terminals.
Multi-user berths.
Cone Marine Fenders
Cone fenders are an adaptation of cell fenders and are rising in popularity within the industry. They’re designed to withstand a variety of conditions and are suitable to be used with large vessels - for example, tankers and cruisers. As they’re an adaptation of cell fenders, they’re very similar in construction and share many of the same properties.
Cone fenders are specially designed to withstand high impact from large vessels - their unique conical construction with mounted flanges ensure fender stability. That way, large impact levels are cushioned accordingly and there’s no damage to the boat or the docking conditions. They’re reliable and are proven to be useful in a range of tidal conditions.
Key Fender Features:
Robust and maintains performance for long periods.
High shear stability.
Highly efficient geometry for longevity.
Stable at large compression angles.
Recommended Fender Applications:
Tankers and cruise ships
Dolphins and monopiles.
RoRo and cruise terminals.
Oil facilities.
Cargo berths.
Pneumatic Marine Fenders
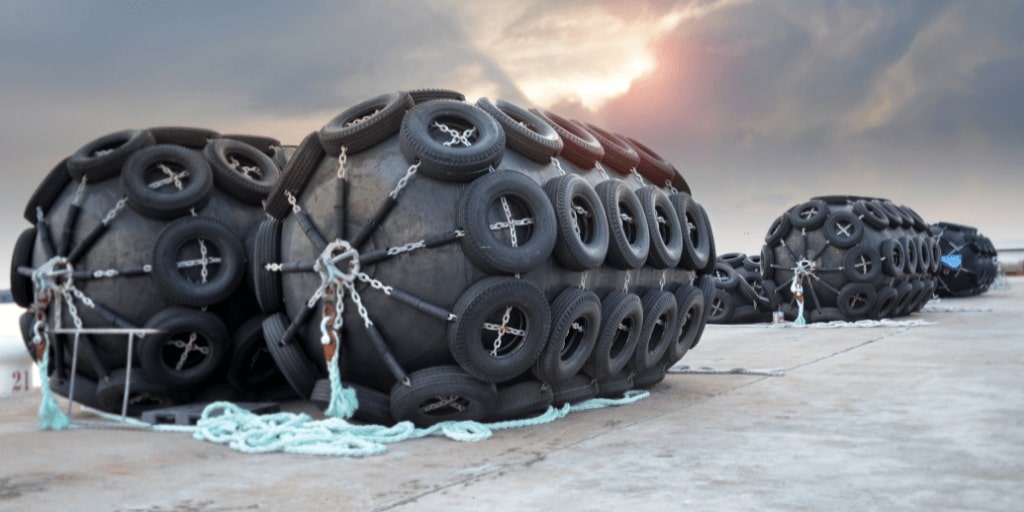
Key Fender Features:
Withstand and absorb forces by inclined berthing at an oblique angle.
Easy to deploy and fast application.
Requires minimal maintenance.
Available in a variety of sizes and types.
Recommended Fender Applications:
In ports with extreme tidal variations.
Ship-to-ship lightering operations.
Oil and gas facilities.
Temporary berthing.
Arch Marine Fenders
Arch marine fenders are mostly used with small or medium-sized vessels. They’re the perfect application for situations in which space is limited or difficult to utilise. An arch fender is one whole shape and either side of the fender is attached to the desired surface - either vertically or horizontally. This allows the fender to cushion high impact levels without any damage.
Although they’re smaller in design than most fenders, arch fenders are still incredibly reliable. Their unique properties allow them to provide excellent protection for vessels and various mooring conditions - even in the most severe circumstances. Plus, they’re flexible and customisable to meet your individual requirements.
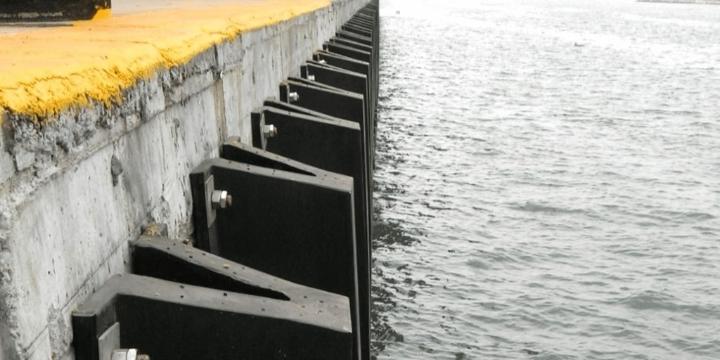
Key Fender Features:
Incredibly strong, simple and durable.
Proven design for safe results.
Single piece rubber moulding for extra compression.
Integrate easily with steel panels.
Available in a variety of sizes.
High durability reduces maintenance operations and implicit costs.
Ideal for situations where mounting space is restricted.
Suitable for multiple marine environments: berths, cargo and harbours.
Recommended Fender Applications:
Cargo berths.
Workboat harbours.
RoRo and cruise terminals.
Barge and tug berthing.
Pile Marine Fenders
Pile fenders ensure a single point contact between the boat and fender application at any water level. They’re highly customisable and have to be specifically designed for individual vessels - that way, they can provide maximum protection. Made up of a single panel, they’re designed to follow a specific vessel’s belting.
You’ll notice that this specific fender type is commonly used in conjunction with a selection of the other fender styles mentioned throughout. Therefore, they’re versatile and can provide adequate protection to a wide range of scenarios. Most commonly, you’ll see them used alongside cone and cell fenders.
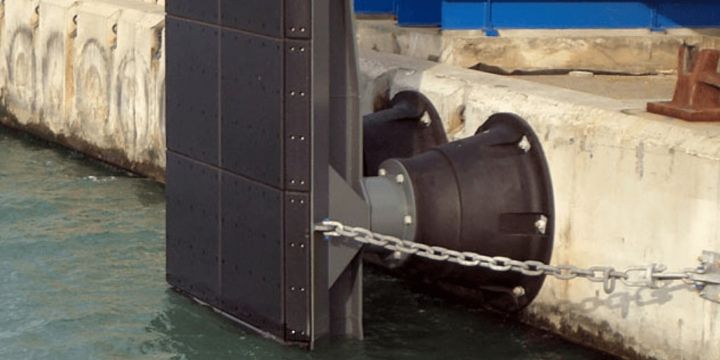
Find Out More About Marine Rubber Fendering - Today!
Now that you’ve learned all about the different types of fendering, it’s time to explore the key manufacturing materials further. As we explained earlier, rubber is one of the most popular material types for fendering applications. But why? What benefits does it bring to the products?
Don’t worry if you’re not sure, we’ve got you covered. Download our FREE guide today to learn about all things marine rubber fendering. That way, when the time comes to choose a suitable fendering application for your needs and requirements, you can make a more well-informed decision.
However, it’s not quite ready yet - we’re just adding the finishing touches. So, in the meantime, please don’t hesitate to contact our expert team. They’re always on hand to answer any questions and queries, plus, alleviate any worries that you may have before purchasing. We look forward to hearing from you.