Rubber for the Oil & Gas Industry
Our role in the oil & gas industry
The oil and gas industry are still one of the largest sectors in the world, forecasting revenue of £4.1 trillion. Naturally, there's a conflict between fossil fuels and renewables. The call to lessen and eventually phase out fossil fuels and transition into a renewable future is for the good of the planet. The renewables sector now has a market value £725 billion in 2020 and will only increase as renewable systems continue to get implemented.
We have been working with the UK offshore energy industry since the oil crisis of 1970. We supply rubber mouldings, extrusions, gaskets and seals to customers throughout the UK and beyond. Our materials and established manufacturing methods create rubber products that are designed to withstand the harshest environments both onshore and offshore. Our oil, gas and renewable industry stakeholders value our exemplary service and fast response times in this evolving sector.
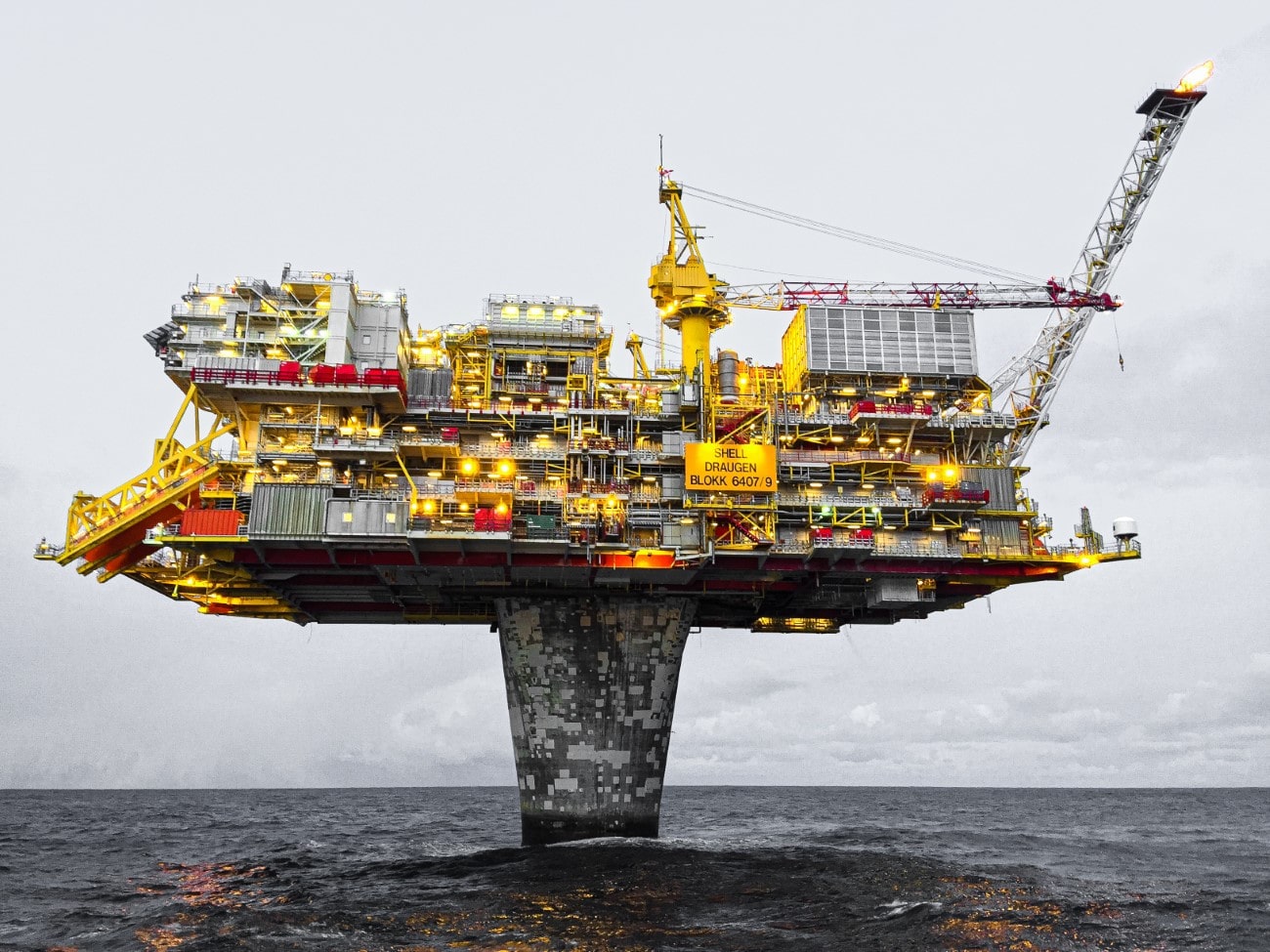
Rubber applications for oil & gas
It’s important to keep your equipment well maintained and protected. Some of the most popular rubber applications in the oil & gas industry are:
- Pipe work flanges
- Hatch seals
- Pontoon fendering
- Dock fendering
- Rig extrusion
- Use of nitrile and neoprene
- Wind farm fendering
- Mooring fendering
Rubber components face extreme conditions. The most common being; prolonged sun exposure, solar radiation, gale force winds, as well as high temperatures from geothermal heat pumps. Rubber is key to protecting sensitive electronic components, and these must be highly effective for optimal performance. The severity of these extreme environments makes the selection of the right material and precise manufacturing processes essential to the long-term performance of the whole system.
We understand the importance of choosing the right material and method of manufacture. Given our wealth of experience in this field, we are well placed to help you select the most appropriate materials, and the optimal manufacturing methods for your specific application needs.
Rubber applications for oil & gas
It’s important to keep your equipment well maintained and protected. Some of the most popular rubber applications in the oil & gas industry are:
- Pipe work flanges
- Hatch seals
- Pontoon fendering
- Dock fendering
- Rig extrusion
- Use of nitrile and neoprene
- Wind farm fendering
- Mooring fendering
Rubber components face extreme conditions. The most common being; prolonged sun exposure, solar radiation, gale force winds, as well as high temperatures from geothermal heat pumps. Rubber is key to protecting sensitive electronic components, and these must be highly effective for optimal performance. The severity of these extreme environments makes the selection of the right material and precise manufacturing processes essential to the long-term performance of the whole system.
We understand the importance of choosing the right material and method of manufacture. Given our wealth of experience in this field, we are well placed to help you select the most appropriate materials, and the optimal manufacturing methods for your specific application needs.
Oil & GasRubber pipe flange gaskets
Oil and gas are finite resources that cannot be wasted, as the practices to extract them are always under close scrutiny. Our rubber flange gaskets can assist your pipelines by closing up those microscopic areas that cause leakages. Connect multiple lengths of piping and keep them sealed and spillage free with our rubber pipe flange gaskets.
Did you know...?
Many hostile industrial environments are found in the maritime sector. Loading and unloading oil tankers at sea, through tethered buoys, is incredibly arduous. Constant movement, 24 hours a day, through storms, differing currents and tides means rubber components need to be durable, long-lasting and designed and manufactured to the highest standards.
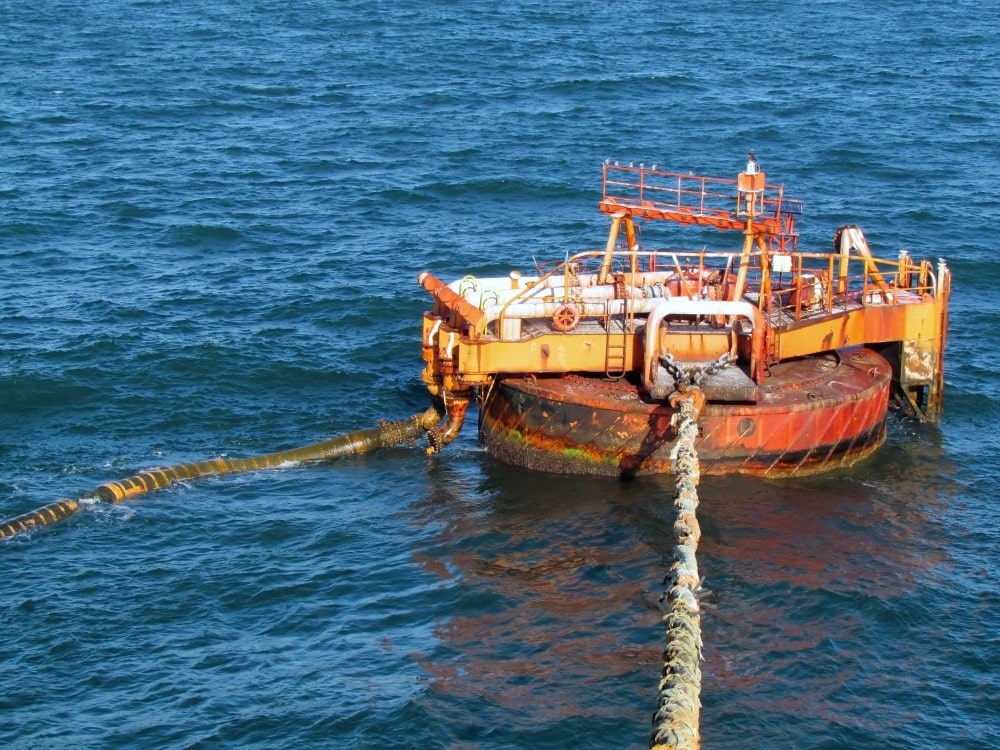
The Walker Rubber Difference

Delivery
Rubber products manufactured to order with industry leading turnaround times.

Support
Not quite sure what you need? Our team are on hand to provide fast, high-quality expertise with years of experience to back it up.

Service
Your journey with us starts in sales. Like our exceptional manufacturing lead times, our sales team is no different. They will guide you through the process every step of the way. We are proud to say 90% of enquiries are quoted on the same day ensuring there is no delay in getting your project with us underway.

Quality
With our right first-time ethos, combined with only using premium materials from trusted sources, the quality of our rubber products are the best in the business.
Our Capabilities
Extrusion
We are experts in the manufacture of rubber extrusions. Our limitations are very small we can produce extrusions from 1m to 10,000m in length or 1mm to 300mm across.
Rubber ExtrusionsGaskets
Our selection of cutting machinery enables us to be accurate and precise, meeting the required specifications for our customers.
Rubber GasketsMouldings
Most moulding requirements are unique to each customer. We supply a comprehensive range of mouldings in a variety of compounds: EPDM, Neoprene, Natural, Nitrile Silicone, Viton, Polyurethane and TPE.
Rubber MouldingsBonding
One of our more unique capabilities. We can bond together multiple types of rubber sheet to create your ideal material.
Rubber BondingTooling
We have the capability to manufacture tooling inhouse, turning your ideas into reality with a short but cost-effective turnaround
Rubber Tooling