How do you make rubber adhesive?
Rubber Adhesion
Adhesives are a substance used to bond or hold materials together. An adhesive material is defined as a “non-metallic binder that acts via adhesion and cohesion.”
Rubber can be used as an adhesive. To successfully bond two substrate materials together, the rubber adhesive must be liquid at the point of application and turn to a solid after the cure. The curing of rubber adhesives involves the solidification through the formation of new crosslinks. (See Curing).
Let's look at how adhesives can be used to bond two substrate surfaces to each other.
Rubber adhesive and cohesive forces
Both adhesive and cohesive forces act upon the adhesive and are determined by intermolecular interactions. The adhesive forces are caused by the interaction of molecules from the adhesive with molecules from the substrate surface. These forces describe the ability of the adhesive to adhere (stick) to the surface. The cohesion forces, on the other hand, are caused by the chemical bonds and intermolecular attraction between the adhesive molecules. These attractions are what hold the adhesive material itself together. An adhesive material must have both strong adhesive and cohesive forces. There is no point in the adhesive being very strongly bonded to the substrate if the material itself cannot handle the loads placed upon it.
A phenomenon which is related to cohesive forces is surface tension. The surface tension of a liquid is due to the cohesive forces within the bulk of the material and is defined as the energy required to increase the surface area of the liquid adhesive. Within the bulk of the liquid, the molecules will be evenly distributed. This means, that molecules in the bulk of the liquid are surrounded by molecules at an equal distance and will experience equal intermolecular forces from all directions.
The molecules on the surface, however, will be attracted to the molecules within the bulk of the adhesive. Stronger cohesive bonds tend to minimise the surface area, hence increasing the surface tension. Strong adhesive forces and surface tension is what causes droplets of liquids to assume a spherical shape. Different liquids will have different surface tensions.
What are polar molecules?
Polar molecules are molecules with an uneven charge distribution. The adhesive forces are caused by intermolecular interactions. These interactions depend on whether the molecules are polar on non-polar.
In covalent bonds, the shared pair of electrons will sometimes be held slightly closer to some atoms than others. This is due to the electronegativity of the atoms. This uneven distribution of electrons within a molecule will cause one end of the molecule to become slightly negatively charged and the other to become slightly positively charged. These polar molecules are called dipoles.
The slightly negatively charged atoms in the dipole will be attracted to the slightly positively charged atoms in neighbouring dipoles. These intermolecular interactions can only occur at very small distances (less than 0.5 nm) and so the adhesive material must be able to make close contact with the surface.
What are non-polar molecules?
Non-Polar molecules are molecules with shared electrons evenly distributed between the atoms. For example, electrons are held at an equal distance between hydrogen and carbon atoms. This means that hydrocarbon rubbers such as Natural rubber, SBR, BR, EPDM and IIR are non-polar.
The forces between non-polar molecules are weaker than dipole-dipole forces and are known as London dispersion forces. These occur due to the random movement of electrons which can lead to the formation of a temporary dipole within the molecule. This uneven charged molecule will induce dipoles in neighbouring molecules, by repulsing like charges.
Polar molecules will be attracted to other polar molecules via dipole-dipole forces. Non-polar molecules will be attracted to other non-polar molecules via London Dispersion forces. Polar and non-polar molecules, however, will not be attracted to each other. It is therefore important to ensure that the chosen adhesive is compatible with the substrate material.
What is the wetting process?
Wetting is the spreading of liquid over a solid substance. The adhesive and the substrate are held together by lots of weak electrostatic forces. This means that for maximum adhesion, the adhesive should be completely spread over the substrate to increase the contact surface area between the two substances. The wetting of an adhesive is its ability to form an interface with the solid surface. The degree of wetting, also known as wettability, depends on both the surface tension and the viscosity of the adhesive. This can be determined by the contact angle between the substrate and the adhesive as shown below.
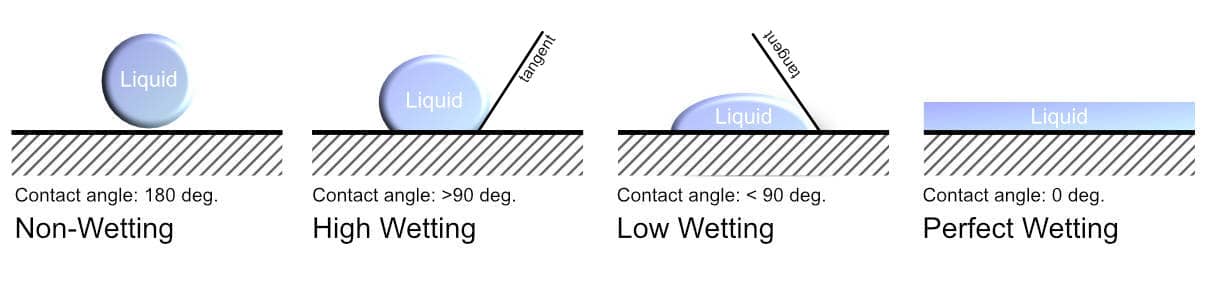
The wettability of an adhesive is determined by a force balance between adhesive and cohesive forces. When the cohesive forces within the liquid are greater than the adhesive forces, then the adhesive will retain a spherical shape. This is known as de-wetting. On the other hand, when the adhesive forces outweigh the cohesive forces, the adhesive will be attracted to the substrate surface. This leads to wetting which is the spreading of the liquid on the surface of the solid.
Substrate materials with low surface energy do not wet out easily as there will be a lower adhesive force between the liquid and surface. As a rule of thumb, the higher the surface energy the higher the strength of adhesion. The surface energies of some typical materials are shown in the table below.
Material | Surface energy (mN/m) |
---|---|
PTFE | 15 |
Silicone Rubber | 26 |
PE/PP | 30 |
Hydrocarbon Rubbers | 30-40 |
PU | 45 |
PA | 45 |
Glass | 100 |
Metals | ~500 |
To ensure the wetting of the material, the surface tension of the adhesive must be less than the surface energy of the solid surface. The surface tension of selected liquids is shown in the following table.
Material | Surface tension (mN/m) |
---|---|
Ethanol | 22 |
MEK | 24 |
Toluene | 28 |
Water | 70 |
Mercury | 500 |
Another factor which determines the wetting of a substrate is the viscosity of the liquid adhesive. The viscosity of a fluid depends on the strength of its intermolecular forces between its molecules. The greater the attraction between the molecules the more viscous the liquid will be. High viscosity adhesives can be advantages as this can help to avoid the running of the adhesive at the edges of bonded joints.
The wetting of an adhesive increases the surface area between the substrate and adhesive materials. The surface area can also be increased by Mechanical Interlocking, illustrated below. This occurs when the adhesive penetrates any pores or irregularities in the substrate surface. The interlocking also helps to provide a physical barrier which can limit crack propagation at the interface.
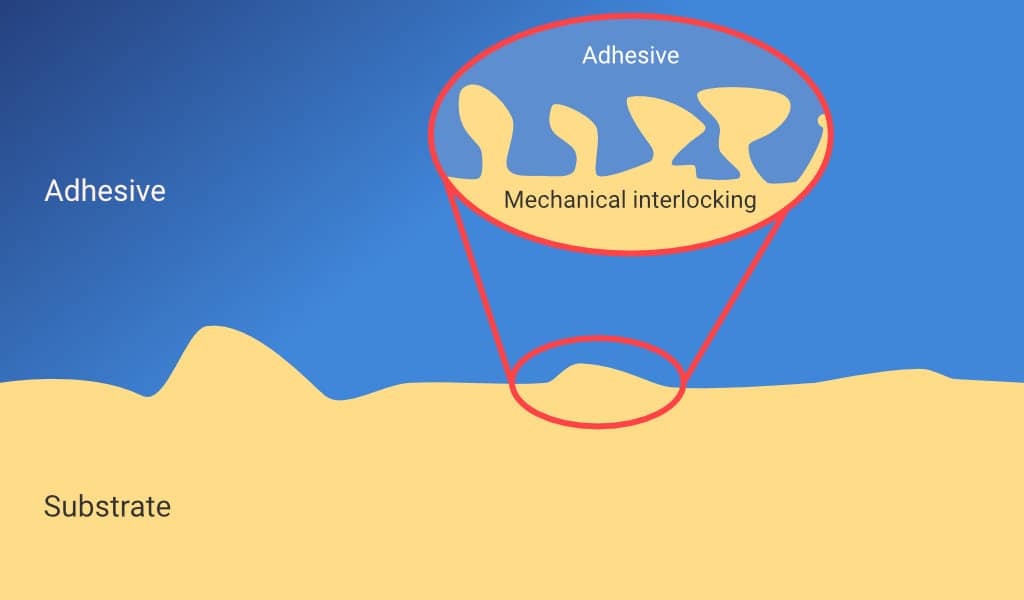
Which rubbers can be bonded?
The list below depicts the rubbers that can be bonded ordered by their ease of bonding, 1 being the easiest and 7 being the hardest to bond.
- Nitrile Rubber (NBR)
- Chloroprene Rubber (CR)
- Styrene Butadiene Rubber (SBR)
- Natural Rubber (NR) / Isoprene Rubber (IR)
- Polybutadiene Rubber (BR)
- Ethylene Propylene Diene Rubber (EPDM)
- Butyl Rubber (IIR)
Due to their low surface energy and chemical inertness EPDM and Silicone rubber can be incredibly challenging to bond. The adhesive selection is critical in these applications to ensure good bonding of these materials.
How can the level of adhesion be improved?
A number of steps must be taken to ensure good bonding between the adhesive and substrate. The strength of an adhesive bond can be improved by:
- Selecting an appropriate adhesive (for the chemistry of the substrate surface)
- Ensuring adequate preparation and pre-treatment of substrate
- Carrying out bonding process properly
- Using an adhesion promoter or primer
Why is my rubber not bonding?
The most common cause of bond failure is the contamination of the bonding surfaces. To avoid this, the substrate surface must be cleaned thoroughly before they are bonded. Potential surface contaminants include oil, greases, and dirt. Ingredients in the rubber compounds such as waxes, plasticisers and process aids can also lead to contamination and ultimately weakening of the bond.
Rubber adhesive primers
Adhesive primers are a surface coating which are often used to pre-treat the substrate surfaces before the adhesive is applied. Primers are used to increase the strength of the adhesive bond and can be used to help adhesives bond to different surfaces. Pre-treating the substrate surface, often improves the adhesive's ability to wet out the surface. This can help the adhesive to bond to metals, plastics, or materials with low surface energy which it would not otherwise create a strong bond with. Primers can also be used to protect corrosion sensitive surfaces.
Primers are especially useful for use on porous surfaces that otherwise tend to absorb the adhesive. Adhesive primers are also used to strengthen the bond for products designed for environments where the temperature is consistently below zero degrees.
Primers are often formulated to be used on a specific substrate material or in conjunction with a particular adhesive. Adhesive primers are available as a paint or a spray which can be easily applied to the substrate material. The primer should be applied to the surfaces as evenly as possible. Most primers dry within 1 - 3 hours. The substrate must be properly cleaned and dried before the application of the primer to avoid contaminants.
How to prepare a surface for bonding
To successfully remove all potential surface contaminants the Degrease-Abrade-Degrease procedure should be followed. The first degrease removes inherent surface contaminants from the surface. The substrate can then be abraded (worn down), either mechanically or chemically. This is an essential step as it increases the surface area of the surface and provides a mechanical key for interlocking. Finally, a second degrease is required to remove any contaminants left by the abradant.
The primer or adhesive must then be applied to the substate within a short time window, to minimise the contamination from the environment or air.