Measuring Rubber Hardness
What is the hardness of rubber?
Hardness is the measure of the material's resistance to scratching, abrasion and indentation. The hardness of a rubber describes how firm or soft the material is.
Rubber hardness is an important factor in product design and is often one of the first properties to be considered when selecting a material. The desired hardness of the material will be based on its intended application.

Why use hard materials?
Hard materials are chosen to achieve high resistance to surface penetration, offering the utmost protection. Harder materials will be more durable and tend to offer a greater resistance to wear either by friction or erosion in reaction to steam, oil, and water. This makes hard rubbers a suitable choice for applications such as caster wheels or heavy-duty construction-based equipment.
Hard materials should always be on top of the list when dealing with high pressure and heavy loading. Softer compounds on the other hand are often chosen for gaskets and O-rings as these products stretch easier and seal better on rough surfaces due to their high elasticity.
Gaskets must be as soft as possible in order to completely fill the space between the two surfaces. They also must be strong enough to resist the lateral forces acting on them. The hardness of rubber can be used as an indication of the material's resistance to bending or rigidity.
How is material hardness measured?
There are three types of material hardness which can be measured:
- Indentation hardness - The resistance of the material to its localised plastic deformation.
- Rebound/dynamic hardness - The elastic hardness of a material. The rebound hardness measures the energy absorbed by the material on impact which is returned to the indenter. Courtesy of the rubber elasticity, the material regains its original shape and is not permanently deformed.
- Scratch hardness - The material's ability to resist surface scratches.
There are various tests which can be carried out to measure the hardness of engineering materials and the hardness can be expressed on many scales such as Brinell (HB), Rockwell Hardness, Leeb hardness value or Vickers Hardness (HV). The hardness of elastomers is usually determined using the Shore Hardness Scales or the International Rubber Hardness Degree (IRHD) scale. On all scales, a higher number indicates a harder material.
Shore hardness scales
Shore scales can be used as a method of measuring and comparing the hardness of rubbers and elastomers. They are also commonly used for softer plastics such as polyolefins, fluoropolymers, and vinyl. There are around fifteen different shore hardness scales which can be used to measure the hardness of the different materials.
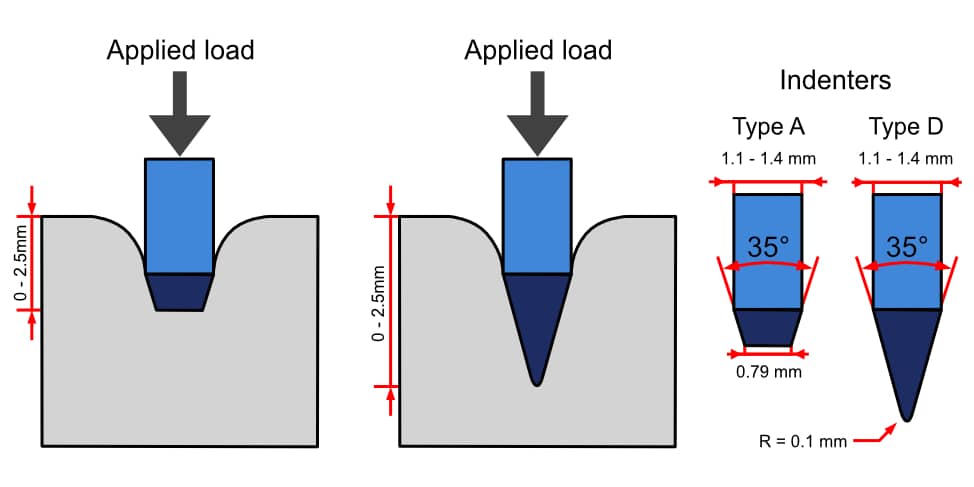
The Shore A scale is most commonly used for measuring the hardness of rubbers and can be determined using a durometer gauge. The durometer consists of a metal truncated cone indenter, attached to a small spring as shown in the diagram above the indenter is extended 2.5mm into the material. The material will resist the indentation, deflecting the spring. Every 0.001 inch that the spring is deflected relates to 1-degree shore A. Harder materials will resist the indentation, this will cause the deflection of the spring to be higher and will result in a higher reading. The diagram below gives a representation of each of the shore hardness values. Shore 70 A is the standard hardness for rubber.
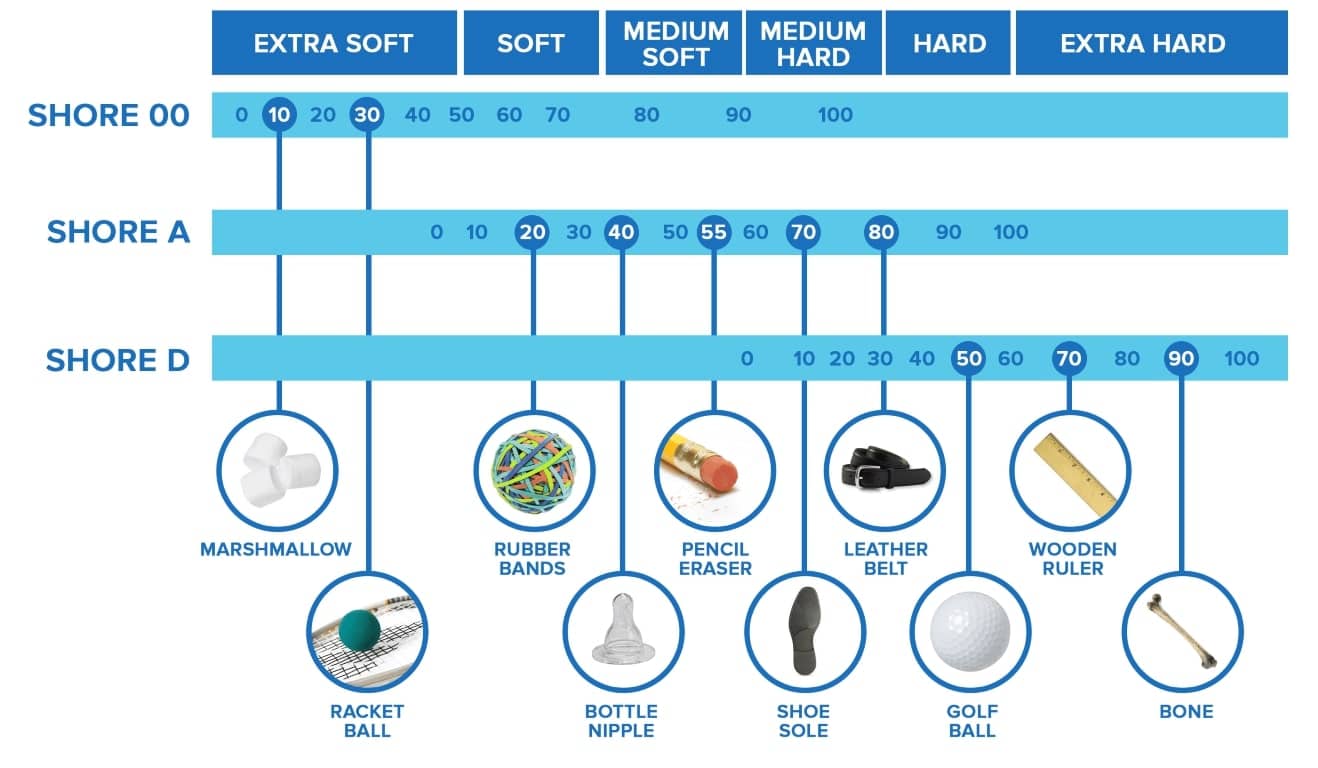
The great thing about the shore hardness scale is that you can measure any material. This scale has been adapted to meet the needs or requirements for any material measurement. The Shore A scale is often used for measuring softer rubbers and the Shore D scale is used for harder ones. The shore D scale was developed to measure the hardness of hard rubbers which have a value of over 90 degrees on the Shore A scale. Similarly, shore 0 was introduced to measure the hardness of soft rubbers which record less than 10 degrees on the Shore A scale. Shore 00 was introduced for very soft rubbers or gels which recorded less than 10 degrees on the shore 0 scale. Shore B and Shore C are intermediate scales intended for use on medium and moderately hard rubbers. A comparison of Shore Scales A, D, 0 and 00 are given in the table below.
The shape of the indenter that is used on the durometer and the spring force vary by scale. For example, shore D uses a sharply pointed indenter and a spring force of 10lbs (4.5 kg) whereas the indenter for shore 00 has a blunt point and a spring force of only 113g.
Shore hardness testing will often leave a permanent indentation in the test sample. Another consideration is that the material must be at least 6mm thick and positioned on a hard surface to get an accurate reading. If the material is too thin, the durometer will measure the hardness of the surface on which the material is placed. Due to the mechanical limits of the test instruments, hardness measurements in elastomers are normally expressed in 5-degree increments.
Shore 00 | Shore 0 | Shore A | Shore D |
---|---|---|---|
Medium and Low-Density Cellular Elastomers, Urethane Foam and Cork | Medium Density Cellular and Solid Elastomers | Solid and Cellular Elastomers | Polyurethanes, PTFE rigid, Thermoplastic and Elastomeric, very hard |
100 | 58 | ||
95 | 46 | ||
90 | 39 | ||
85 | 33 | ||
98 | 84 | 80 | 29 |
97 | 79 | 75 | 25 |
95 | 75 | 70 | 22 |
94 | 72 | 65 | 19 |
93 | 69 | 60 | 16 |
91 | 65 | 55 | 14 |
90 | 61 | 50 | 12 |
88 | 57 | 45 | 10 |
86 | 53 | 40 | 8 |
83 | 48 | 35 | 7 |
80 | 42 | 30 | 6 |
76 | 35 | 25 | |
70 | 28 | 20 | |
63 | 21 | 15 | |
55 | 14 | 10 | |
45 | 8 | 5 |
International Rubber Hardness Degree (IRHD)
Like shore hardness, IRHD testing results in measurements between 0 and 100. The difference is that the value on the IRHD scale is non-linear and is related to Young's Modulus (modulus of elasticity in tension or compression) of the material. The IRHD scale is chosen so that a material with Young's Modulus of zero will be represented by 0 IHRD hardness and a material with infinite Youngs modulus will correspond to a hardness of 100.
There are four methods of carrying out the test depending on the hardness range of the rubber.
- Normal hardness test - for rubbers within the hardness range of 30 - 95 IRHD.
- High hardness test - for rubbers within the hardness range of 85 - 100 IRHD.
- Low hardness test - for rubbers within the hardness range of 10 - 35 IRHD.
- Micro test - a scaled down version of the normal test, for rubbers within the hardness range of 35 - 85 IRHD.
How is IRHD measured?
The International Rubber Hardness Degree is measured by indenting a spherical ball into a material sample under two different loads. The difference in the depth of indentation under both loads is measured.
IRHD is a non-destructive method of testing hardness, and it will not leave an indentation in the rubber. The IRHD micro test can be carried out on materials between 1 and 5mm thick. The micro test is the ideal method for testing thin products such as O-rings. This is beneficial as it will give a value of hardness for the particular product and not just for the material used. It has been found that the shape of the material does not greatly affect the overall hardness of the product.
Both IRHD and shore scales give measurements of hardness on a scale of 0 - 100 degrees. The difference between these two methods comes from the fact that the Shore Scales are linear, based on the deflection of the rubber, whereas IRHD is a non-linear scale related to the elastic modulus of the material. For highly elastic rubbers, Shore A and IRHD give comparable values. A comparison of hardness values for IRHD and Shore A Hardness is shown in the table below.
Shore A | IRHD |
---|---|
100 | 100 |
95 | 95 |
90 | 90 |
85 | 85 |
80 | 80 |
75 | 74 |
70 | 68 |
65 | 64 |
60 | 62 |
55 | 54 |
50 | 49 |
45 | 44 |
40 | 39 |
35 | 35 |
30 | 28 |
25 | |
20 | |
15 | |
10 | |
5 |