What is Rubber Compounding?
Rubber Compounds
A rubber compound is a raw rubber mixed with another chemical substance that will increase the potential and performance of the rubber. A perfect example of this is vulcanisation, the chemical added is sulphur that creates crosslinks which hardens and improves the elasticity of the rubber.
In this section we'll looking at rubber compounds which include the vulcanising elements, fillers and pigments that can change the colour of the rubber.
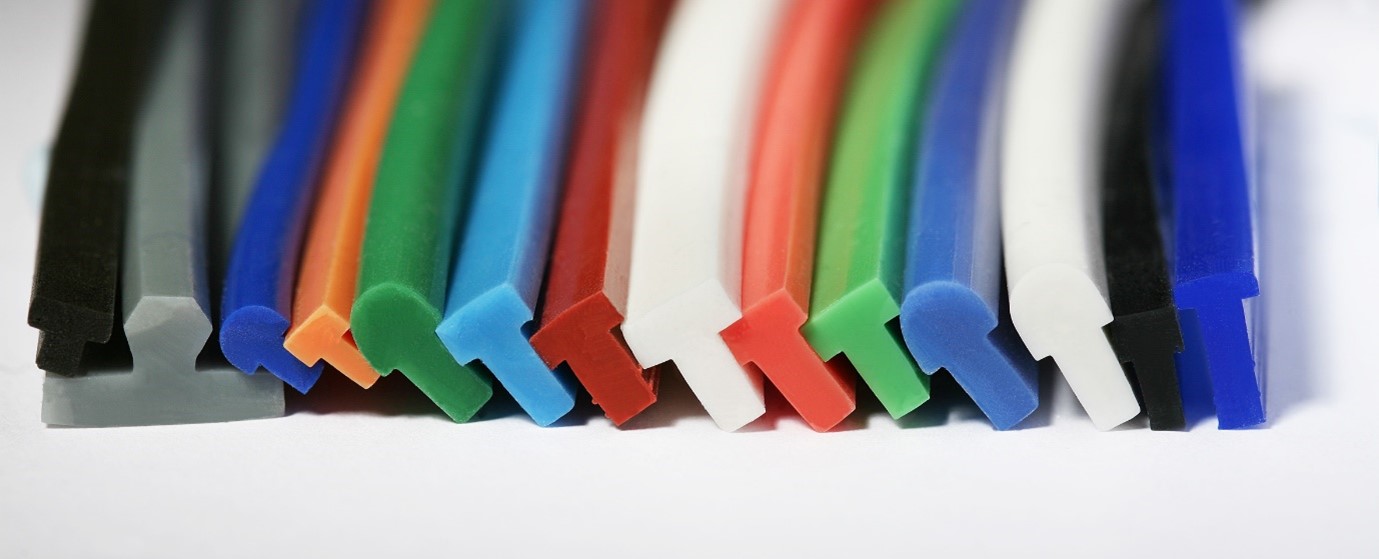
What is rubber compounding?
A compound is a mixture of chemicals which are added together to combine their desired properties. Rubbers on their own have limited commercial application due to their mechanical properties one for which being a lack of elasticity. These properties can be improved through vulcanisation / curing and crosslinks. Another way to improve rubber properties is by adding different materials to the rubber in a compound.
Rubber compounding is a complicated science, rubber technologists need a very technical background to be able to create successful compounds. The materials be chosen wisely and the ratio of the ingredients must be chosen specifically to reach the desired properties of the final product. It can take hundreds of iterations to perfect. Each ingredient in the compound has a specific role and affects the final rubber product. Ingredients can be added to the base rubber compounds to improve its mechanical properties, processability or to reduce the cost. The quantity of each ingredient in the compound is expressed per 100 parts.
What ingredients are in a rubber compound?
The basic ingredients used are, the rubber and the vulcanising agent. The rubber is the base of the compound and provides the main rubbery qualities of the final mixture. Usually, sulphur or peroxide is added as the vulcanising agent. Other vulcanising agents include amines, silanes, and anilines. These chemicals cause crosslinks to form in the rubber. To learn more about this process, read our article on Curing.
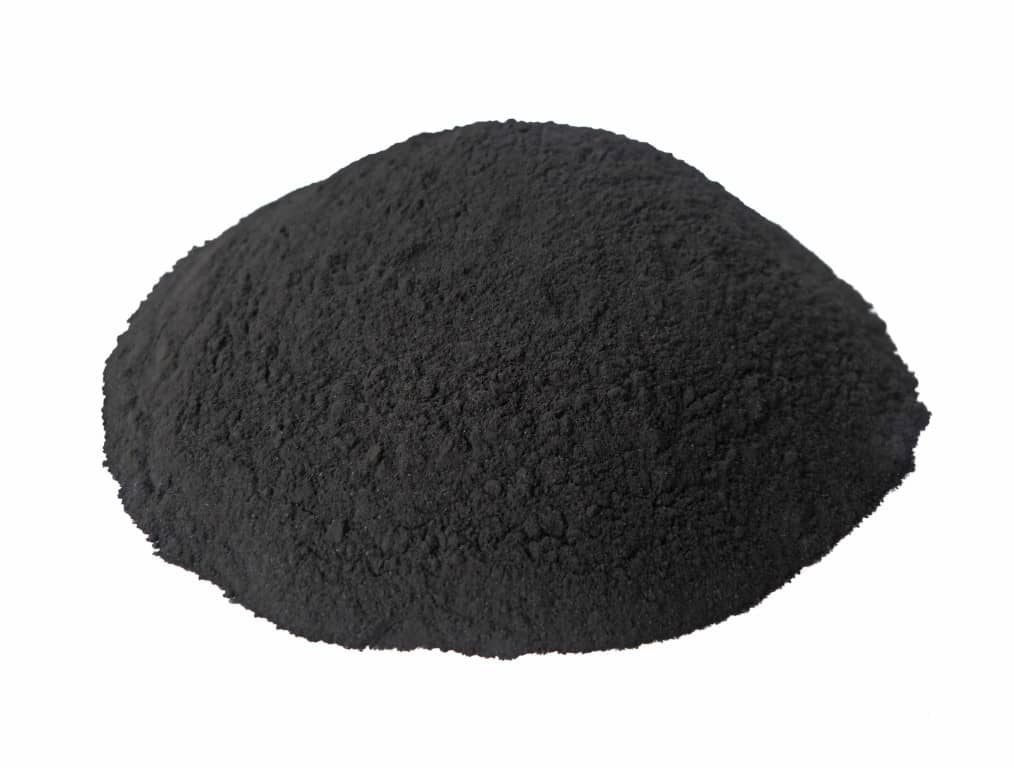
How do you strengthen rubber?
The strength of rubber can be improved by adding a reinforcing filler such as Carbon Black to the compound. Carbon Black, shown in the diagram above, is a powder containing fine particles of mainly carbon, produced by incomplete combustion. Carbon Black has nanoparticles with various functions such as ultraviolet absorption and conductivity. The particle and structure size of the Carbon Black can affect its dispersibility and blackness. In general, increasing the size of the particle or the structure will decrease the blackness of the compound but will improve the dispersibility of the particles.
How does carbon black strengthen rubber?
Carbon Black increases the strength, abrasion resistance and weathering properties as it absorbs harmful UV radiation. Adding Carbon Black to the compound can cause the material to become brittle. To counterbalance this, oils such as processing, or extender oils are added to the compound.
These can also be referred to as plasticisers, softeners, or processing aids. The addition of the oils helps to incorporate the dry ingredients and can also make the resulting material easier to process by reducing its viscosity. Most rubber compounds contain a significant amount of these oils as well as Carbon Black to increase the strength of the material as much as possible without stiffening the material. The ratio of Carbon Black to oil must be chosen carefully depending on the intended purpose of the rubber.
Most rubbers are black in colour due to the addition of Carbon Black. Other reinforcing fillers including white clays and mineral fillers and pigments can be used to create coloured compounds, but white fillers usually offer less reinforcement than Carbon Black.
What chemicals can improve a rubber compound?
Chemicals such as zinc oxide and stearic acids can be added to the compound. These chemicals are known as accelerators or activators as they can speed up the reaction of vulcanization. The traditional method of sulphur curing developed by Goodyear used to take hours but with the addition of accelerators, it can now be done in minutes.
How do you control the rubber vulcanisation process?
There are ways to manage the vulcanisation of rubber, with the use of accelerators, activators and retarders. Speeding up the vulcanisation reaction from hours to a few minutes significantly decreases the processing time of the rubber material. It's important to use these accelerators wisely as they make the vulcanisation reaction super-fast. The crosslinks are formed before the rubber has been shaped into its final form and the accelerators run the risk of scorching the material. To allow time for the rubber to be shaped properly before the vulcanisation occurs, “retarders” are added to the compound. Retarders delay the crosslinking reaction until the rubber mixture is at the curing temperature.
What are antioxidants and antiozonants?
Antioxidants help protect the compound from high temperatures while in use and while the compound is being mixed. These ingredients can absorb free radicals in the air that can break the polymers bonds and reduce service life of the compound. Antiozonants protect the compound from the ozone, creating an impenetrable barrier surrounding the rubber. Carbon black has antiozonant properties.
A rubber compound can become a very complicated and intricate mixture including rubber polymers, reinforcing fillers, accelerators, retarders, antioxidants, and antiozonants. Each of these ingredients and their ratios can influence the final material. Rubber compounders require a lot of skill and knowledge to create successful mixtures. The rubber compounds can be manipulated in many ways to tailor the compound for their specific job. For example, compounds can be influenced into having high oil resistance, higher abrasion resistance, higher operating temperatures or lower compression set.
How do you change the color of rubber?
To change the colour of a rubber, coloured pigments can be added to the compound. Selecting a colour can be complicated and is normally carried out by a qualified colour technician. The colour can often be the most expensive ingredient in a compound. There are different types of colourants available depending on the intended use of the rubber. For example, more durable colourants should be used if the rubber is intended to be used outdoors.
When selecting a colourant, it is also important to consider the other ingredients in the compound. White clay and mineral fillers must be used in coloured compounds which tend to be less reinforcing than Carbon Black and do not offer the same level of UV protection. Neoprene is available in a variety of colours and is the go-to non-black rubber compound on the market, offering the same levels of durability.
What is rubber mixing?
The ingredients in a compound are combined in a process called Mixing. This process is a critical part of manufacturing rubber. Mixing must be well controlled. Consistent and conducted by a colour technician to achieve the desired properties of the rubber formulation.
Good dispersion and distribution of the materials within the compound are essential in achieving good quality and uniform final products. The distribution of a compound refers to how uniformly mixed the particles from different materials are and the overall homogeneity of the rubber material. With optimal distribution, the particles from each material will be as far as possible from each other. The dispersion instead describes how uniform the particles are. If they are clumped together this means that they are not adequately dispersed. Solid materials like fillers, must be broken down to achieve optimum dispersion. It is possible for a compound to be well distributed but poorly dispersed and vice versa. This is shown in the image below.
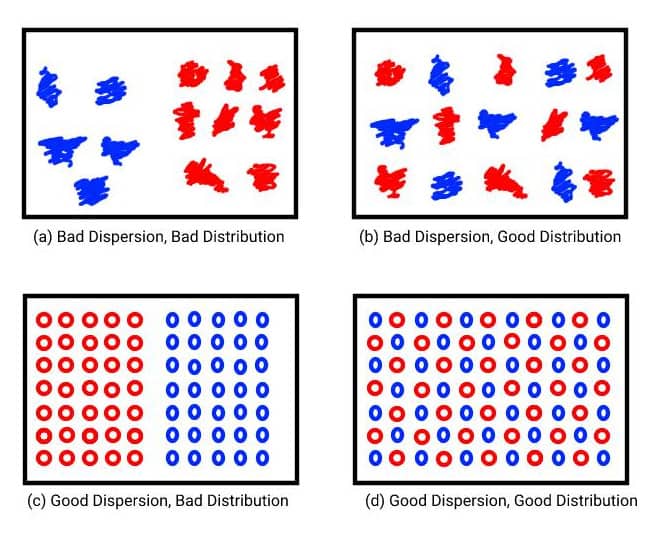
What is internal rubber mixing?
In an internal mixer, the compounded materials are added together in a chamber via a hopper, which has two rotors inside. These rotors can generate shear forces which mix the compound ingredients. This method effectively disperses and distributes the particles within the compound and results in a uniform and high-quality end product.
Internal mixers such as an 'Intermix' or 'Banbury' are industrial machines for compounding rubber ingredients.
For complex formulations, the mixing process is usually carried out in stages. Initially, the rubber material will be added to the chamber on its own. The other compounding ingredients will then be added one at a time to the mixer.
What is open mill rubber mixing?
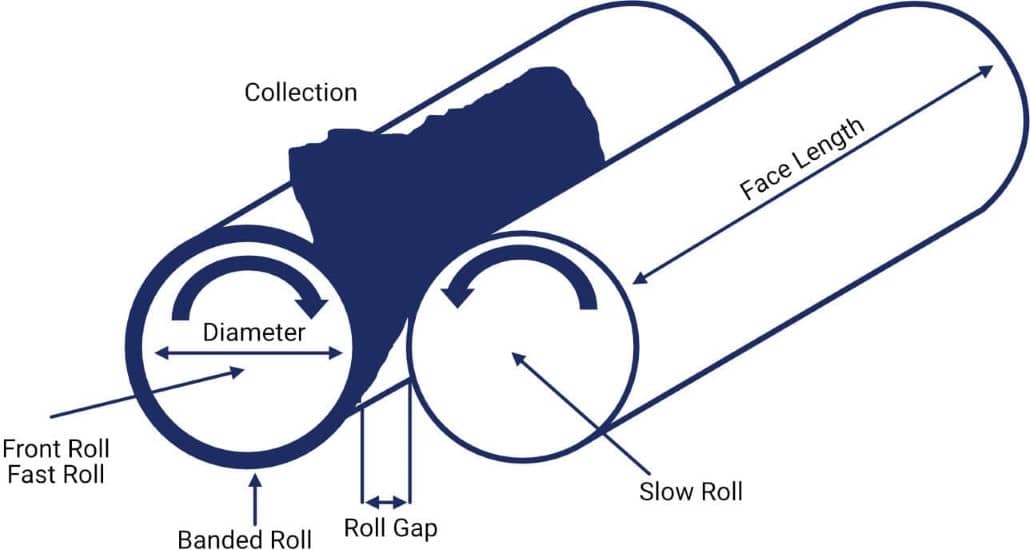
Open Mills can be used for both the mastication of rubber and the mixing of rubber compounds. The open mill mix consists of two exposed horizontal metal rolls. These rolls rotate in opposite directions as shown in the diagram above. The rubber is bonded onto the front roll. The raw materials for the compound are then added at the nip. The back roll spins slower than the front one, exerting shear forces on the rubber. The speed ratio (or friction ratio) between the two rolls is variable and can be set for each particular rubber formulation.
The advantages of open mill mixing are:
- Dispersion of the batch is higher
- Mastication of the rubber is higher
- Can be used for two-stage mixing
The disadvantages of open mill mixing are:
- Takes longer than internal mixing
- Consumes larger amounts of energy
What are tandem mixers?
Tandem mixers aim to optimise both the dispersion and distribution of particles in rubber compounds. They achieve this by connecting two different mixers in series and separating the tasks of dispersion and distribution. The first mixer disperses the compound, and the second mixer distributes it. The final compound is then processed in an open mill and processed as normal.
What are material grades for rubber?
The material grade indicates the compound composition and the overall quality of the rubber. Depending on how the compound was made, the rubber will exhibit different material properties. This means that it is especially important to select rubber of a suitable composition. These rubbers exhibit different behaviours and to account for this, they are split into grades. There are many grades available of both synthetic and natural rubbers.
The grade of a synthetic rubber will be dependent on the types and quantities of raw materials used in the compound. In natural rubber, impurity levels, collection methods and the process techniques used can all affect the quality of the final rubber product. International standards and guidelines for natural rubber quality can be found in the “Green Book” published by the Rubber Manufacturers Association in the USA.
Material grades are introduced in various industries to ensure the safety and protection of the end consumer. Any rubber product created in these grades must be compliant with rules and regulations that are specific to that material grade. These grades are used in industries like:
- Food
- Medical
- Pharmaceutical
- Water
Commercial grades, food grades, medical and pharmaceutical grades of rubber are approved to be used in specific situations.
What is the food grade for rubber?
Food grades are certifications of approval, enforced by regulatory agencies to ensure the safety of the general populous. In America, the standards of food grade rubber are set by the Food and Drug Administration (FDA). There are no standardised EU regulations for food-grade rubber, but there are national regulations set out by the government in France, the Netherlands, Italy, and Germany. It’s imperative that any rubber product which will have contact with food, foodstuff or food additives has no contaminants passed onto the food. Certain rubber compounds can contain polymerisation aids, catalysts, plasticisers, and additives which could potentially be transferred to the food on contact.
The guidelines state that the rubber used for food should be safely used in:
- Producing
- Manufacturing
- Packing
- Processing
- Preparing
- Treating
- Packaging
- Transporting
Food grade rubbers should be used in all products throughout the manufacturing of food and are typically used in belting or seals. Rubbers that are approved by the FDA for these purposes include grades of:
- EPDM
- Silicone
- Nitrile
- Neoprene
Silicone rubber is the most commonly used synthetic rubber in the food and beverage industry due to its versatility. It can withstand high temperatures, is impervious to liquids, odourless, non-toxic and durable.
What is the medical grade for rubber?
Medical-grade rubber is certified by regulatory agencies around the world for the safety of the general public. For FDA Standards, the final product must receive FDA approval rather than the individual materials themselves. The FDA has produced a Whitelist of chemicals which have been approved for use with selective percentages present in the compound.
In the medical industry, rubber goes through higher and more thorough testing measures than food grade. The level of testing required depends on the intended use of the final product and the drugs that it will interact with. These compounds must be biocompatible and must not cause adverse reactions within the human body or prevent any medicines from working effectively.
Rubber can be used for a variety of different purposes within the medical environment ranging from dust covers for surgical equipment to components of implanted medical devices such as pacemakers and medical device components such as seals in syringes and IV penetration tubes.
Any rubber used in this environment will need to withstand potent active pharmaceutical ingredients and aggressive cleaning regimes. Silicone rubber is the better material choice for these applications and is commonly used in cannulas and surgical breast implants.
Medical grade rubbers include:
- EPDM
- Silicone
- Nitrile
- Neoprene
Natural rubber contains latex and is no longer used in most medical facilities due to healthcare workers suffering from anaphylaxis. Synthetic rubber is the safer option and does a much better job with regards to durability, longevity and being impermeable.
What is the pharmaceutical grade for rubber?
Pharmaceutical-grade rubbers are certified by regulatory agencies preventing any possible contamination or tainting of pharmaceuticals or medicines. For FDA Standards, the final product must receive FDA approval rather than the individual materials themselves. The FDA has produced a Whitelist of chemicals which have been approved for use with selective percentages present in the compound.
Following a similar path as medical grade rubber, pharmaceutical grade rubber must be non-toxic, long-lasting, both heat and cold-resistant and unable to contaminate any medicines or drugs. In this industry, rubber compounds are used in the assembly processes for transporting medicinal substances.
Any rubber used in this environment will need to withstand potent active pharmaceutical ingredients and aggressive cleaning regimes.
Medical grade rubbers include:
- EPDM
- Silicone
- Nitrile
- Neoprene
Nitrile and Silicone are the most commonly used rubbers in the pharmaceutical industry. Both rubbers have different properties:
Nitrile for example can be used in water, is impermeable to gas, has a natural resistance to abrasions and is resistant to oil and petrol. It recovers well after being put under pressure.
Silicone is also good for use with water, is non-toxic, can be used with natural gases due to its resistance, also recovers well and has a resistance to ozone exposure.
What is WRAS?
Water Regulations Advisory Scheme (WRAS) approval is provided to materials and products which are safe for use within potable water applications for human consumption. WRAS-approved rubbers must be specifically formulated and manufactured to ensure they will not contaminate water.
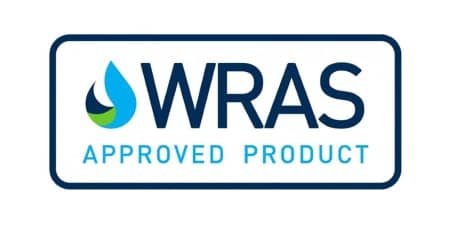
Can rubber contaminate?
Materials can contaminate water through the migration of toxic chemicals or by creating conditions that encourage the growth of bacteria. Some materials may pass a taste or smell to the water as well as cause cloudiness or decolouration.
To ensure safe drinking water, WRAS grades of rubber should be used in any product within the water supply system, including the transportation and storage of water. Rubber is often used in water pumps or as seals and washers within pipework.
Guidelines for the materials used in water fittings and plumbing systems are outlined by the government in Water Supply (Water Fittings) Regulations 1999. Using WRAS approved materials shows awareness and a willingness to comply and develop products that will not contaminate water.
Products with WRAS approval are issued with a WRAS certification mark. WRAS grades are available for Nitrile and EPDM rubbers.